Brass milling is a common process in the manufacturing industry, but how does it compare to milling other metals? This article explores the differences between brass milling and milling other metals, providing insights into materials, machining techniques, applications, and more.
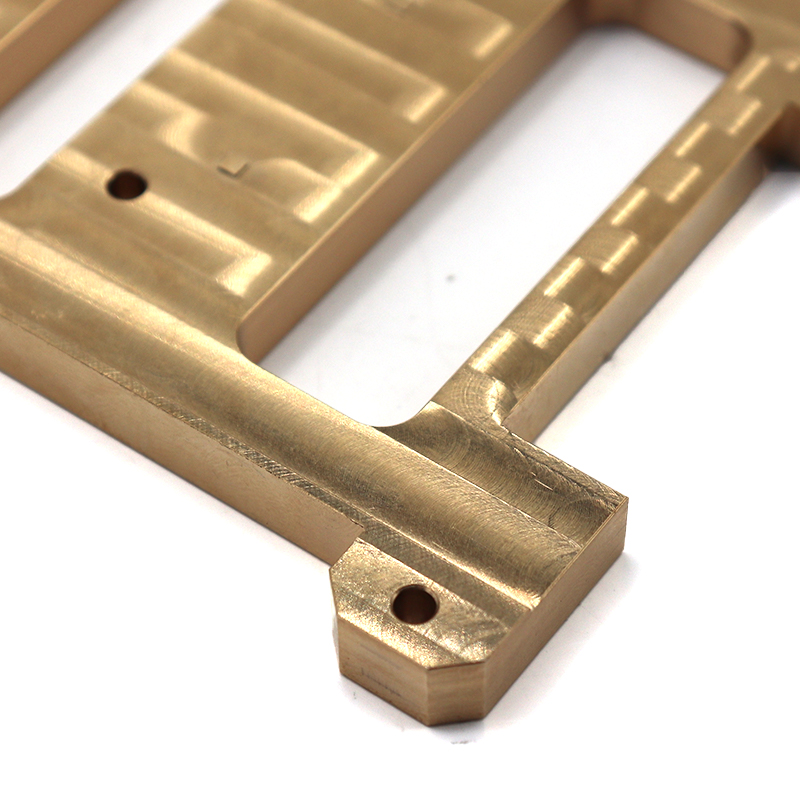
Table of Contents
ToggleBrass Milling vs. Other Metal Milling: What You Need to Know
1. Brass milling Basics
Brass, an alloy of copper and zinc, is valued for its excellent machinability, corrosion resistance, and aesthetic appeal. brass milling involves the removal of material from a brass workpiece to create custom components with precise dimensions and surface finish. CNC machining is often used for brass milling due to its accuracy and efficiency.
2. Brass milling Characteristics
– Machinability: Brass is known for its exceptional machinability, allowing for high-speed cutting and efficient chip removal.
– Surface Finish: brass milling typically results in a smooth surface finish, requiring minimal post-processing.
– Corrosion Resistance: Brass exhibits good corrosion resistance, making it suitable for applications in harsh environments.
– Workpiece Stability: Brass workpieces are generally stable during milling, with minimal risk of warping or deformation.
3. Brass milling vs. Other Metal Milling
Brass vs. Aluminum Milling
– Material Properties: Brass is denser and softer than aluminum, requiring different cutting parameters and tooling.
– Machinability: Brass generally offers better machinability than aluminum, with lower tool wear and smoother surface finish.
– Applications: Brass is commonly used in applications requiring corrosion resistance and aesthetic appeal, while aluminum is preferred for lightweight and high-strength applications.
Brass vs. Steel Milling
– Material Hardness: Steel is significantly harder than brass, requiring tougher tooling and slower cutting speeds.
– Machinability: Brass is easier to machine than steel, resulting in faster machining times and lower production costs.
– Applications: Steel is preferred for applications requiring high strength and durability, while brass is suitable for parts requiring corrosion resistance and electrical conductivity.
4. Applications of brass milling
brass milling finds applications in various industries, including:
– Electronics: Brass components are used in electrical connectors, terminals, and circuit boards.
– Automotive: Brass parts are found in automotive fittings, valves, and fuel system components.
– Plumbing: Brass fittings, valves, and pipe connectors are common in plumbing applications.
– Decorative: Brass is used for architectural hardware, decorative fixtures, and ornamental components.
5. Brass milling Techniques
– Tool Selection: Carbide or high-speed steel (HSS) tools are commonly used for brass milling, with geometry optimized for chip evacuation and surface finish.
– Cutting Parameters: brass milling requires moderate cutting speeds and feeds to prevent tool wear and maintain surface quality.
– Coolant Usage: Coolants, such as water-soluble oils, are used to dissipate heat and lubricate the cutting tool during brass milling.
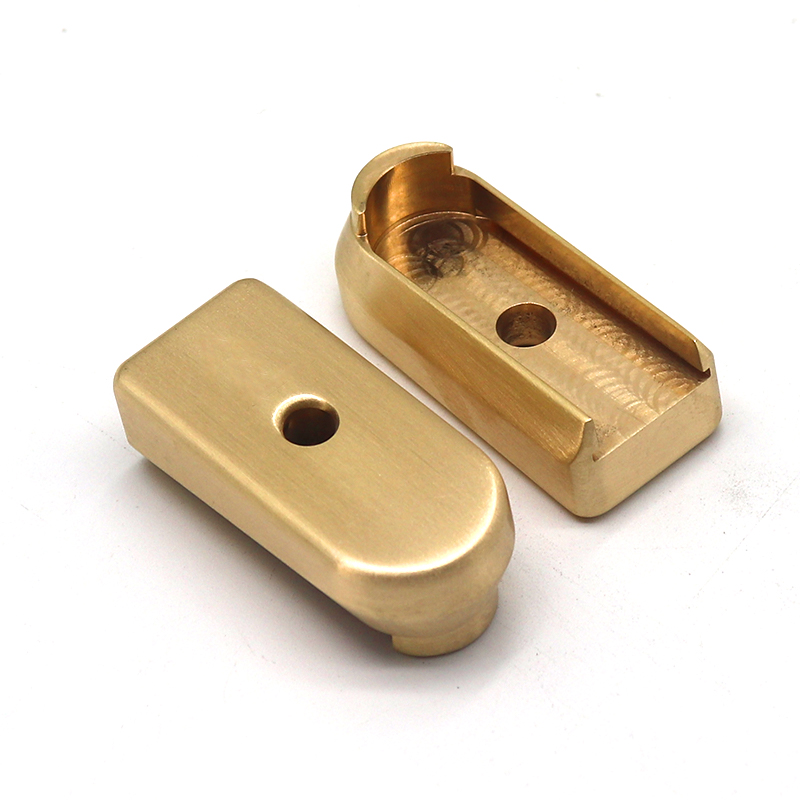
6. FAQ
Q: Is brass milling suitable for high-volume production?
A: Yes, brass milling is well-suited for high-volume production due to its excellent machinability and relatively low material cost.
Q: Can brass milling produce intricate parts with tight tolerances?
A: Yes, CNC machining enables brass milling to produce complex parts with tight tolerances and precise dimensions.
Q: What surface finishes can be achieved with brass milling?
A: brass milling can achieve a range of surface finishes, from standard milled to polished or brushed finishes, depending on the application requirements.
Q: Are there any environmental considerations associated with brass milling?
A: Brass is a recyclable material, making brass milling an environmentally friendly manufacturing process. Proper disposal of machining waste and coolant management are important for minimizing environmental impact.
Q: How does brass milling compare to other manufacturing methods, such as forging or casting?
A: brass milling offers advantages in terms of design flexibility, precision, and cost-effectiveness compared to forging or casting. However, the choice of manufacturing method depends on factors such as part complexity, production volume, and material properties.
0